2013.12.17
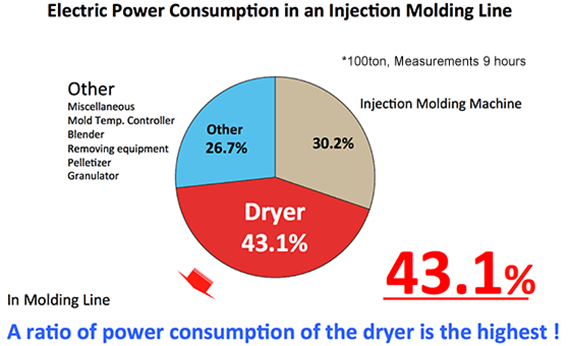
Achieve Green Molding (4)
Continued from my previous article.
Solutions for eliminating Energy Waste
Matsui proposes “factor4” as the primary target in molding factories. As a partner for resource conservation, our goal is to help customers achieve 4-times resource productivity by eliminating waste and increasing output.
In the previous issue, we were looking for the “Waste of Energy” lurking in molding factories. Using the illustration I suggested improvements through simple changes. For example; reviewing equipment layout, reducing hose lengths and switching to insulated hoses, mold plates and Cylinder Jackets…
Today, I will talk about machinery and equipment that has yet to be mentioned. We often think only of molding machines when imagining a plastics molding factory. However when a closer look is taken, we can see there are many other systems and support equipment needed. Perhaps you remember this power consumption graph which illustrates the breakdown of electrical use inside a typical molding cell.
The results shown here come from data collected during testing in real molding plants. Surprisingly, the biggest consumer of energy in most molding cells is not the molding machine, but instead the resin dryer! Therefore focusing on the reduction of dryer energy consumption will lead to the biggest energy savings!
We have worked diligently at developing products which enhance energy efficiency. Although successful, we soon realized these new more capable products alone weren’t enough to achieve factor 4. We decided a more radical approach was needed, and began a review of all molding functions.
Let’s take another look at some illustrations shown previously.
Molding machines don’t run all the time. They can sit idle for a variety of reasons. Sometimes production is stopped to change product color, materials or even the mold itself. Needed maintenance or repairs can shut a molder down without warning. In still other cases there may be a failure in support equipment which can also stop production. So you can see that molding machines can often be idle.
Conventional dryers run at full power, at all times. Even if the molding machine stops, the conventional dryer continues to run a full pace, unless they are manually turned down or off. This is clearly a “Waste of Energy”. Furthermore this situation can degrade the plastic resin by exposing it to heat for an extended period. Referred to as “over-drying”, this unnecessary heat exposure can adversely affect the quality of the molded part.
The MJ5-i was developed with a sharp focus on energy savings and proper drying of the resin. As a result, the MJ5-i can reduce energy consumption by up to 75% over a conventional dryer. I will now explain how this was achieved.
The greatest feature of this new dryer, which contributes to the incredible energy savings, is the intelligence or ‘iplas’ function. iplas automatically adjusts dryer operation by monitoring resin condition. MJ5-i makes it possible to maintain the resin’s proper dry state while keeping energy use to the absolute minimum. With iplas, the MJ5-i autonomously adapts to the operational status of the molding machine.
The chart above shows production molding process. The conventional dryer continues drying at full power, at all times. But the MJ5-i operates in sync with molding process. Automatic adjustments are made (seen as a blue line) to match the operational status of the molding machine and production volume. This is all energy savings.
Another feature of the MJ5-i is the reuse of waste heat. In a conventional dehumidification dryer, hot air used to regenerate desiccant was simply exhausted to plant. Instead, the MJ5-i captures much of this heat energy normally lost with a specially designed heat exchanger.
As a result of iplas & design features like capturing & reusing waste heat, dryer energy-savings of up to 75% are realized. But benefits grow beyond the dryer energy use. Plant air conditioning systems don’t have to work as hard because less heat is exhausted by dryers.
(We also offer energy saving kits for your existing dryers. These kits will help eliminate the “Waste of Energy” and start you on your way to achieving factor 4!
Please feel free to contact us! )
By identifying and offering these improvements along with the MJ5-i, “green molding” becomes possible; An ideal factory that is kind to people and environment.
To be continued…
- Getting Rid of Wasted Energy