2013.11.18
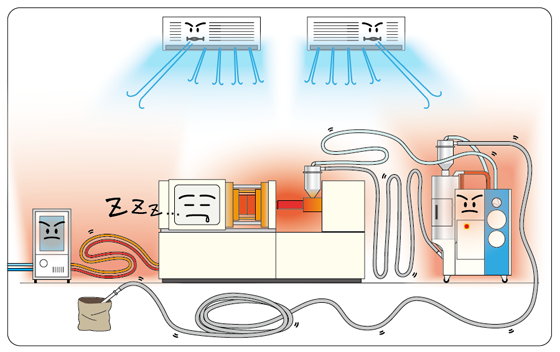
Achieve Green Molding (3)
Continued from my previous article.
Solutions for eliminating Energy Waste
Matsui proposes “factor4” as the primary target in molding factories. As a partner for resource-conservation, our goal is to help customers achieve 4-times resource productivity by eliminating waste.
We discussed “Resin waste” in molding factories in the previous issue. We will now focus on ‘Energy waste’, within this issue.
What kinds energies are used in a molding factories?
A molding machine is required to mold, but this alone cannot produce a plastic product. Temperature control devices are needed for keeping constant mold temperatures, Dryers for conditioning a resin material, Transport systems to move the raw material between devices, and Brenders, Granulators, Conveyer and … various machines are working there.
Those who are working in the factory, please try to imagine the workplace.
Those who are not working in the factory, please refer to the illustration below…
This illustration is simple configuration, but let’s look for “energy waste” in this molding factory.
The molding machine in the center seems to be idle, but the mold and the heating tower are being kept at high temperature, so they are radiating heat energy. The mold temperature controller keeps working, so it is radiating heat energy from the body and piping. The dryer on the right side of the molding machine is radiating heat energy too.
Even though production has been stopped, peripheral devices continue to change thermal energy from electrical energy. And, the air conditioning system operates at full capacity in order to maintain the temperature in the workplace.
What about the pipes connecting the equipment? Considerations for moving the equipment mean hoses + pipes remain longer than necessary. Energy loss due to radiation from long pipes for the temperature control system will consume much energy. Excessive feed hose for material transport system will cause long blower times as well.
How about you? In most factories, you would see a similar sight sight.
What can we do to get rid of this wasted energy?
Where Do You Start? Organize the peripheral devices!
This not only eliminates unnecessary work for operators, piping will be shortened to optimal length by placing the device in an appropriate location. So you can get rid of exhaust heat waste and achieve a reduction in energy consumption during transportation.
I recommend that you use Insulated mold plates and Cylinder Jackets for your molding machine. The insulation plate prevents heat energy losses. The Cylinder Jacket reduces the heat dissipation from the cylinder, and the molding machine can be temperature controlled with the minimum required energy.
It has become clear working place by only these work. Exhaust heat is also suppressed; energy efficiency would have been well.
Now, let’s look again at the graph of “Electric Power Consumption in an Injection Molding Line”, which was introduced on my first issue.
The machine that uses the most energy in the molding factory was, in fact, not a molding machine but the dryer! So, improving dryer efficiency will significantly reduce “Energy waste”.
- Getting Rid of Wasted Energy