2014.05.20
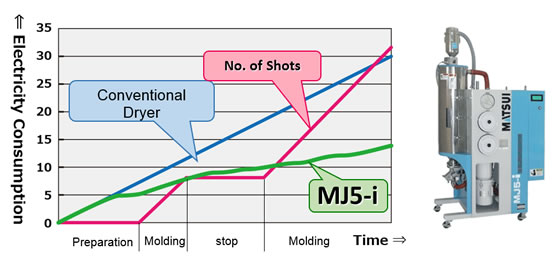
Doubling Wealth & Halving Resource Use” (8) --- Getting Rid of Wasted Energy (2)
7. Preventing Energy Waste (2)
The average resin dryer will waste large amounts electrical energy over its’ lifetime.
As written in my previous article, the reason behind this energy waste, is the basic machine design. Most resin dryers are either on or off.The dryer is either running or it is powered down. Whether the molding cell requires 100% available capacity or 25%, the dryer blindly runs the same way. When a production cell requires 100% of available capacity, this type of dryer design is no problem. But as resin consumption drops in the cell, the potential for the dryer to use energy unnecessarily, rises.
In order to eliminate this waste, it is essential that the dryer be capable of adapting to the varying resin demands. So, how can we adjust drying power without affecting drying performance? Some possible methods;
1. Measure the moisture content of material in the dryer, and reduce drying power to levels just sufficient to maintain the desired moisture level.
2. Measure the mass of resin in the hopper regularly, and adjust drying power to adequate levels for that mass.
However, these methods will require a large amount of time to carry out regular measurements. This will add cost, and offset the attempt to save on energy.
The ‘Adaptive Drying System’ prevents excessive drying of resins
Matsui suggests the following;
3. Control the dry air volume supplied to the hopper dryer, so as to maintain a desired temperature of the air exiting the hopper dryer.
Generally, as dried material is drawn out and fed to process, new “wet” material is loaded into the dryer to replace it. As these new batches of cold material are loaded into the top of the hopper, the drying air stream passing through is cooled. Therefore the more often material is loaded into the hopper dryer, the cooler the air will be exiting the hopper.
It is clear that hopper return air temperature is directly influenced by the consumption rate of materials by the molding process.
Making use of this knowledge, a thermometer can be positioned to measure return air
Temperatures. With this data, drying air flow rates can be controlled to prevent excessive drying. In dehumidifying dryers, this system can be used to achieve energy savings in the regeneration of the absorbent as well. This energy-saving function can also be added to existing dryers as an ‘Option’.;
After adding the ‘Adaptive Drying System’ to some existing dryers, tests showed energy savings of 30~40%! Furthermore, this system requires only the addition of a thermostat, airflow valves and motor speed controls, making the modification affordable.
Dryer modification costs can be recouped within 3 years from the resulting lower energy usage. And when considering the reduced load on plant air conditioning systems, payback can be achieved in an even shorter time period.
Matsui has also developed a new dehumidifying dryer equipped with the above ‘Adaptive Drying System’. To this Matsui added better hopper insulation and a more efficient heat exchanger. This dryer is called the MJ5-i. The graph below shows the difference in energy consumption between a conventional dryer and the MJ5-i. As you can see, the conventional dryer always consumes maximum energy while the energy consumption of the MJ5-i adapted automatically. Depending on whether the injection machine was down for a job change, running at full capacity or moved to a smaller job, the MJ5-i adapted to demand and used less 50% of the energy.
In my next article, I would like to discuss how to prevent energy waste in the water cooling process.
To be continued.
- Getting Rid of Wasted Energy